The painstaking work of scribes in the Middle Ages, patiently copying out works of literature for the great libraries of the monastic orders, is a relic of a bygone age. Today, the multifunction printer is a staple feature of all offices and many homes; it has never been easier to create documents or designs with software such as Microsoft Word or Autodesk’s AutoCAD® tool, and to print them on demand.
It’s remarkable, then, that much of the construction industry still uses a technique more akin to the monastic scribe’s than to the technology of the 21st century. When an architect’s drawing of a building’s floorplan needs to be marked on the floor of the job site, skilled surveyors are normally employed to take measurements, plot the lines and apply markings to the floor by hand. Like the scribe’s handicraft, it is painstaking, skilled, time-consuming and expensive work. And even when performed by professionals, the work is prone to mistakes caused by human error.
HP, the world’s largest manufacturer of printers, saw in this process an opportunity to increase the efficiency and dramatically improve the productivity of this layout process. Its vision was for a combination of its printing expertise with the latest mobile robotics technology. The result was the SitePrint robotic layout solution, the world’s first automated floorplan mobile printer for the construction industry.
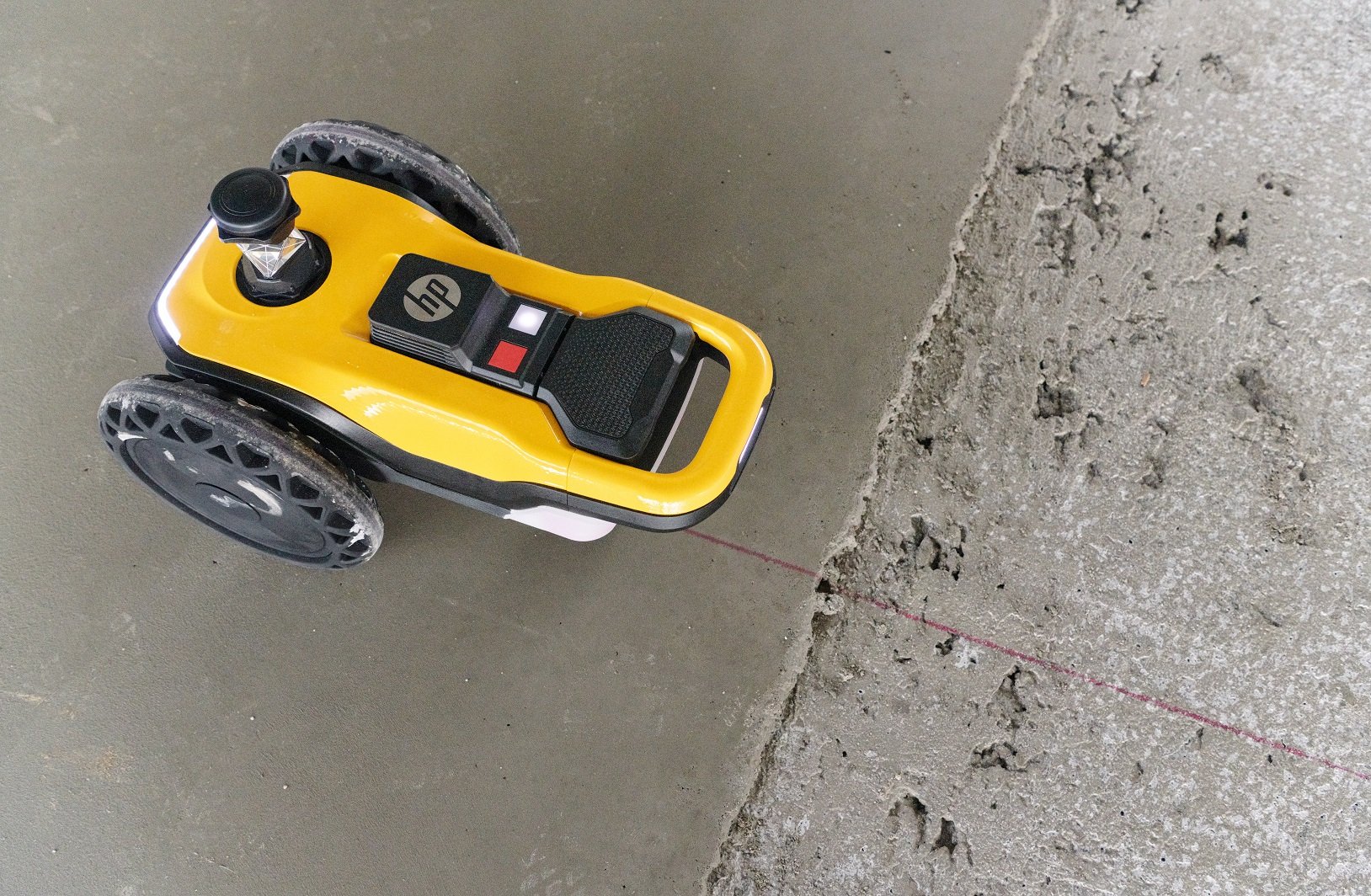
And inside SitePrint is a sophisticated Xsens MTi motion sensor from Movella which keeps the vehicle pointing in the right direction, and ensures that ink is deposited accurately on the floor.
Laser guidance technology
The SitePrint product gives construction companies a fast and easy way to automate layout because it integrates with tools and systems that are already used in most large construction projects today. Before arriving at a job site, a surveyor will download to the SitePrint software a digital plan of the floor from AutoCAD or other familiar design tools. On site, the surveyor connects the SitePrint vehicle to a robotic total station (a standard optical surveying tool) via Bluetooth® or Wi-Fi® wireless. The total station’s laser triangulation system continuously maps the position of the SitePrint vehicle via its tracking prism, and supplies real-time x,y co-ordinates to the vehicle over the wireless communications link.
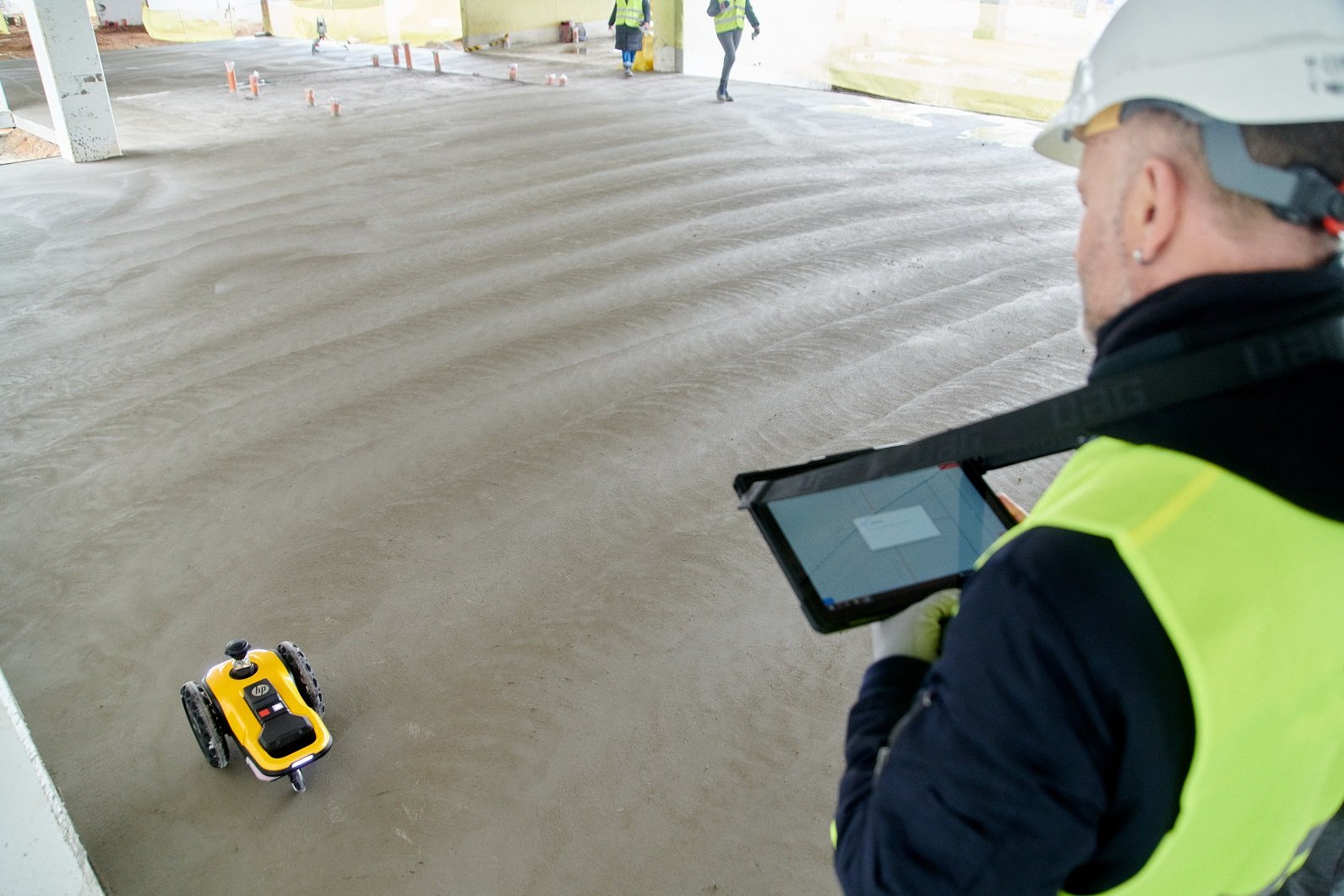
The vehicle compares these x,y co-ordinates with the layout ‘map’ downloaded from AutoCAD to work out where to print markings on the floor. The HP ink technology enables durable layouts to be printed on any compacted or flat surface, including rough concrete, brickwork, timber or screed.
HP says that the printer’s markings are accurate to 3mm. Enabling this high accuracy, the SitePrint vehicle features an Xsens MTi-3, a self-contained AHRS (attitude and heading reference system) module from Movella. This robust, miniature motion sensor provides heading data – showing the direction in which the vehicle is moving – and gyroscope outputs, to give a precise measurement of inclination.
The reliability of the heading data is critically important: the total station link ensures that the SitePrint vehicle’s position is known accurately. But to print a line accurately on the floor, it must also be moving in the right direction. Here, the industry-best magnetic immunity of the MTi family of motion sensors is valuable. Construction sites are full of magnetic interference caused by the presence of large metal objects such as steel joists, electrical cabling and pipework. The MTi-3 is supported by Movella’s unique Magnetic Field Mapper, a magnetic calibration tool supplied to developers as a software development kit (SDK) or as a PC-based application. The Magnetic Field Mapper enabled HP to optimize the SitePrint navigation system for immunity to the type of magnetic interferences generated by the SitePrint itself.
The MTi-3’s gyroscope outputs also accurately gauge the tilt of the vehicle as it passes over surfaces with any kind of slope. The accurate tilt and pan measurements from the MTi-3 ensure that the SitePrint product prints its marks as accurately when tilted as it does when perpendicular.
Automation produces big productivity gains
According to HP product manager Pau Sole, the SitePrint product is set to become the new standard way to perform the layout function in modern construction sites. He says: ‘Automation has increased productivity in many areas of commercial life, but in the construction industry, technology has not had such a profound effect before now. That’s why the SitePrint product is such a breakthrough. Now layout can be completed on-site as much as 10 times faster than before. It also only requires a single surveyor to periodically monitor the operation of the SitePrint vehicle, rather than two surveyors working full-time on manual layout.
‘It’s a game changer for the construction industry, not only because of the productivity and speed improvements. Equally important is the reduced reliance on skilled staff. Surveyors who are qualified to do layout are scarce, and lack of availability of layout surveyors is often a bottleneck that holds up progress on job sites. With the SitePrint technology, construction companies can halve their requirement for surveyors, and free up these skilled professionals to perform other valuable work that cannot so easily be automated.’
Robust, reliable motion sensor for tough building jobs
As the SitePrint product takes on layout tasks in more and more construction sites, it will be exposed to the typical treatment meted out by the building industry. Pau Sole says that the SitePrint design is rugged, to cope with shocks and vibration, and to operate reliably in job sites that are dusty and dirty, and might be extremely hot or cold.
The SitePrint layout solution can handle it all – and with MTi-3 motion data in support, it maintains ultra-high accuracy at all times.
Curious about our product?
You can get to know our products in the product selector.
Product selector