
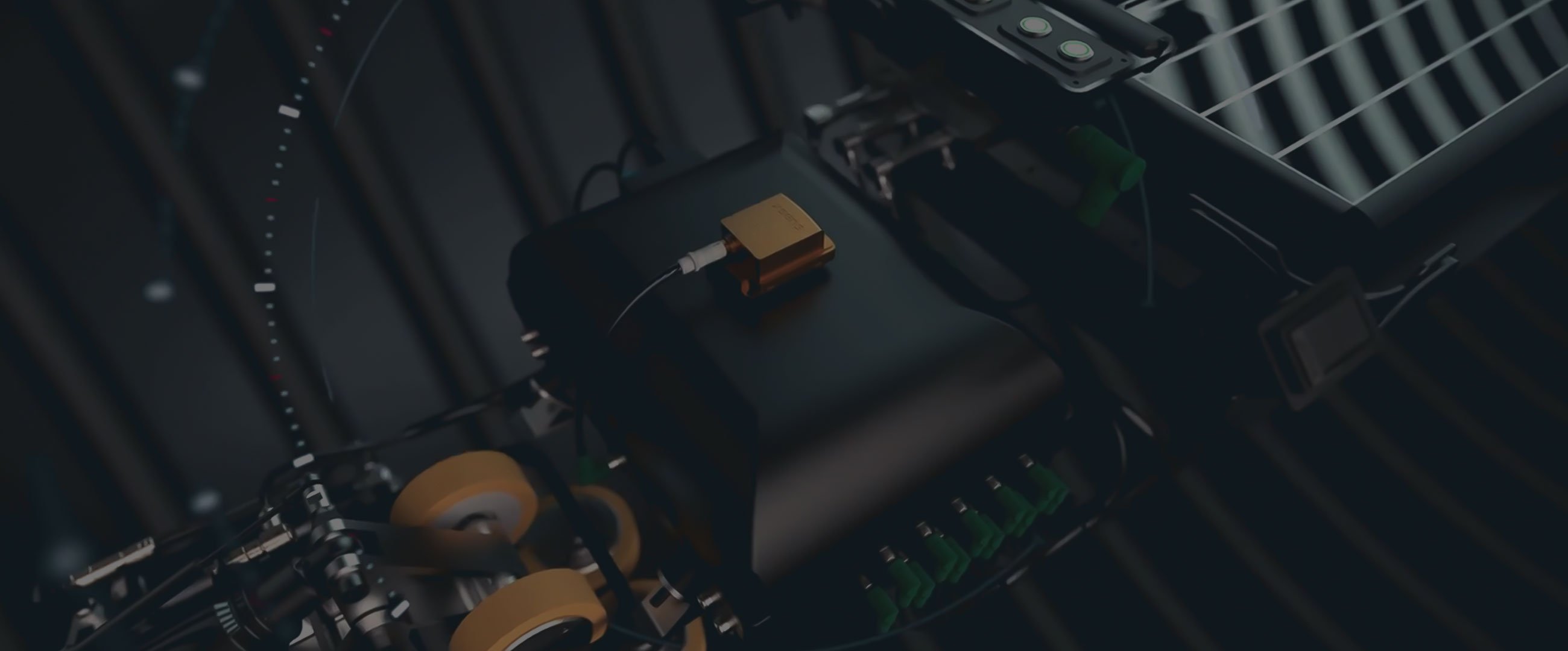
Inertial Measurement Units
Everything you need to know about IMUs
Think of them as the digital equivalent of a human vestibular system, which we use to track the position, orientation and movement of our head in space
Meindert Zeeuw
Director Line of Business Automation & Mobility
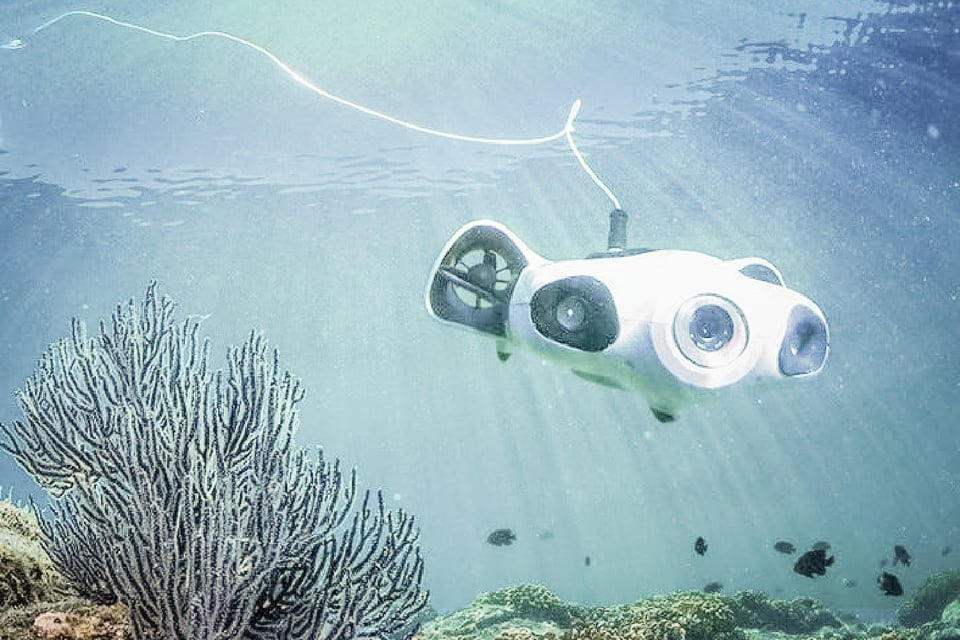
What is an Inertial Measurement Unit (IMU)?
An IMU is a device fitted with multiple components that capture accurate, real-time data of the three-dimensional motion of the object carrying it. This places IMUs at the heart of motion-sensing technology. They are used in a wide range of applications across multiple industries. These include,:
-
Marine applications (surface & subsea), providing navigation and positioning data;
-
Outdoor mobile robots & vehicles, enabling precise movement control;
-
Indoor Autonomous Mobile Robots (AMRs) & Intralogistics, allowing navigation and path planning;
-
3D mobile mapping & surveys, ensuring accurate spatial data collection;
-
Camera, antenna, and payload stabilization, maintaining real-time stability;
-
Automotive testing, for detailed performance data collection;
-
Humanoid robots , assisting in balance and movement control.
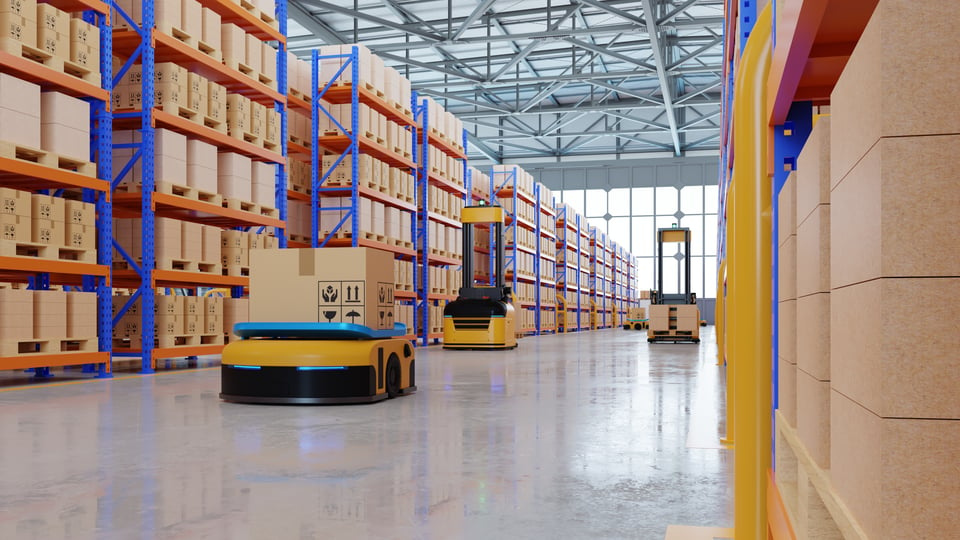
What is inside an IMU?
IMU typically contain three key components:
-
A 3D accelerometer that measures acceleration (m/s2), or velocity changes;
-
A 3D gyroscope that tracks the rate of turn (deg/sec), or angular velocity;
-
A 3D magnetometer that monitors magnetic field data, functioning like a compass and, often used for navigational purposes.
Some IMUs may include a barometer for measuring air pressure to provide altitude data.
Our IMUs
We have several IMUs in our portfolio, from a miniature module to a robust model. Learn more about our IMU navigation and tracking solutions now:
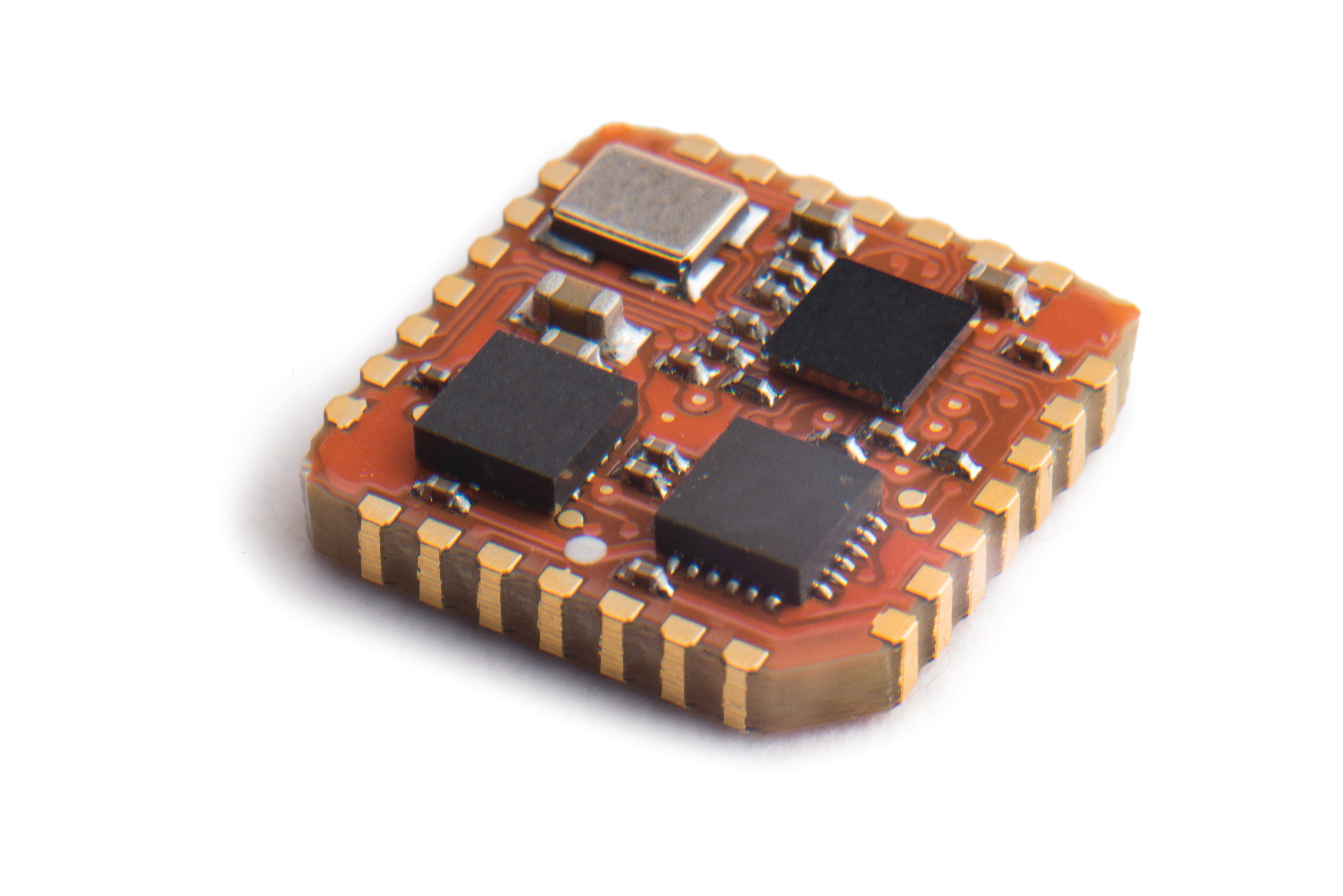
The MTi-1 is a self-contained Inertial Measurement Unit.
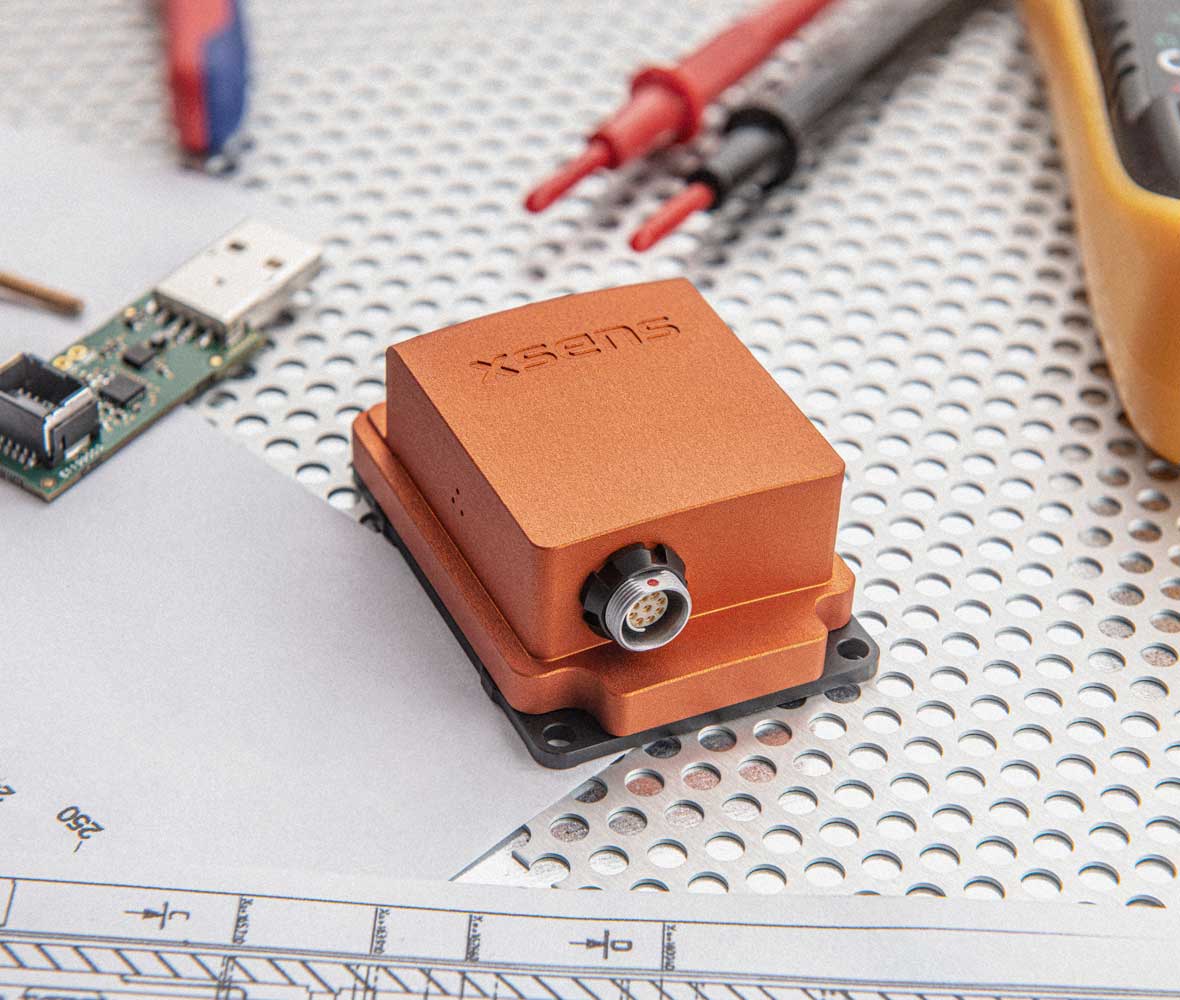
As one of our highest-performing IMU, the all-in-one MTi-100 provides calibrated data on the 3D rate of turn, acceleration and magnetic field.
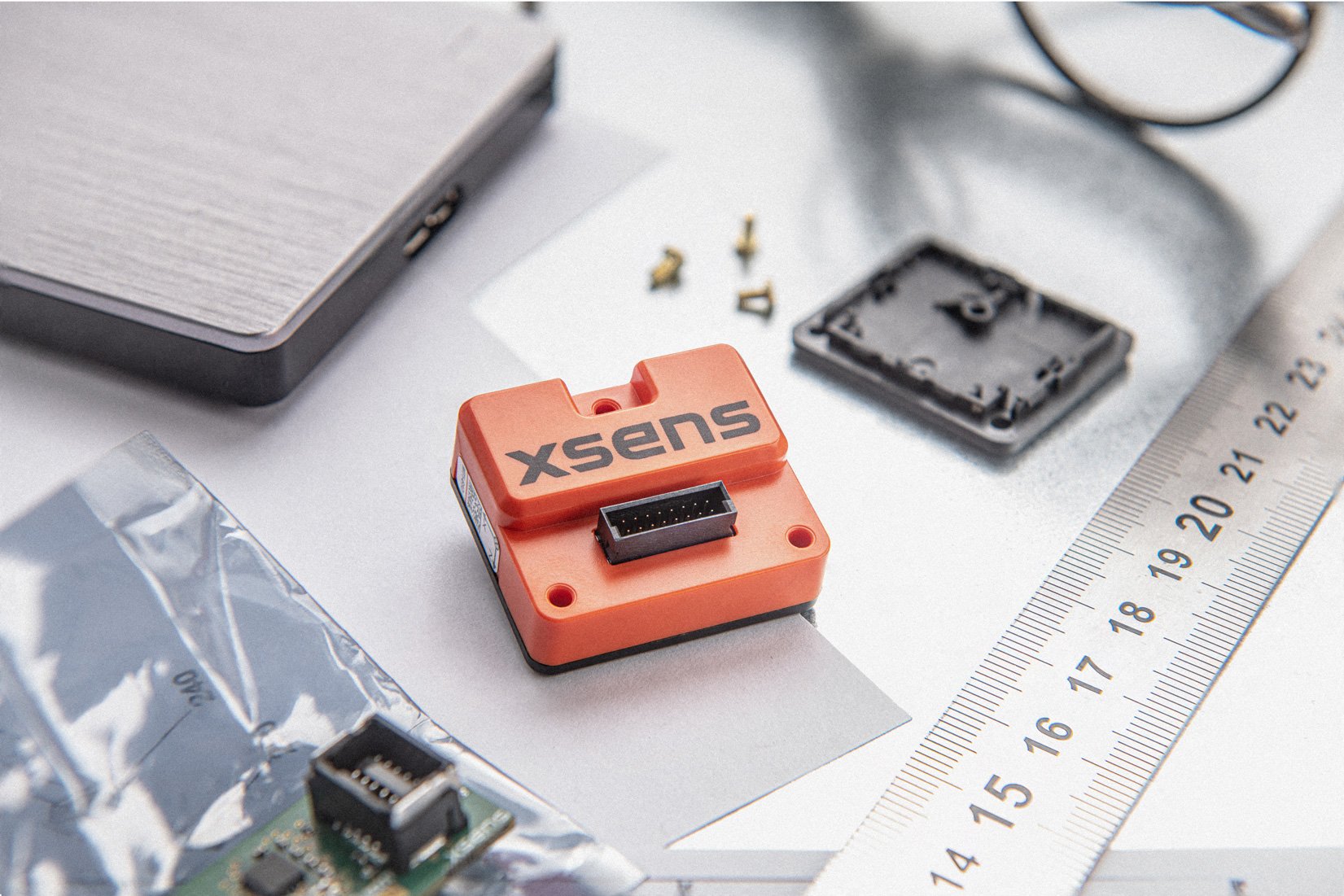
As one of our highest-performing IMU, the all-in-one MTi-610 provides calibrated data on the 3D rate of turn, acceleration and magnetic field.
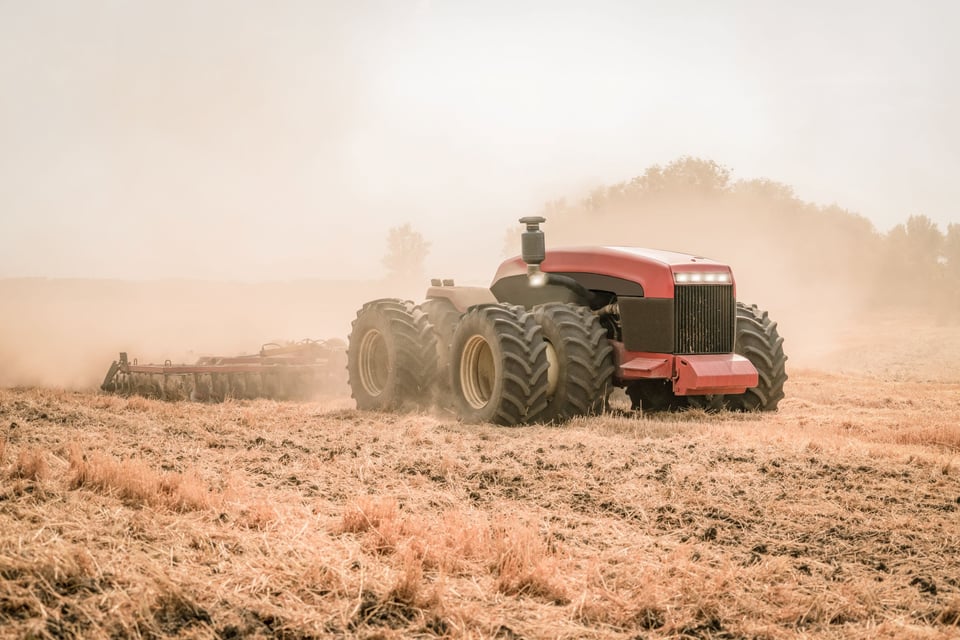
What are an IMU’s capabilities ?
IMUs are indispensable in many industrial applications, especially where precision and stability are crucial. They serve vital functions, such as:
-
Stabilization: IMUs are used in various applications, such as gimbals, to keep cameras, sensors, and other equipment steady, even when in motion. They do this by continuously measuring and compensating for any motion, ensuring stability;
-
Positioning: In applications like antennas, IMUs provide precise, real-time measurements of orientation and positioning. This enables them to make adjustments that will maintain accurate aiming and positioning regardless of external factors.
-
Navigation: Solutions like autonomous vehicles rely on IMUs for precise navigation and movement control. Navigation IMUs gather real-time data on orientation, velocity, and acceleration, providing clear information for accurate direction and movement control. Inertial navigation systems typically feature an IMU and a computational unit.
How does IMU tracking work?
IMU tracking works by combining the three-dimensional motion data from the accelerometer, gyroscope, and magnetometer to accurately track an object’s movement, dynamics, orientation, and direction. Watch Meindert Zeeuw, our Director of Automation & Mobility, explain it.
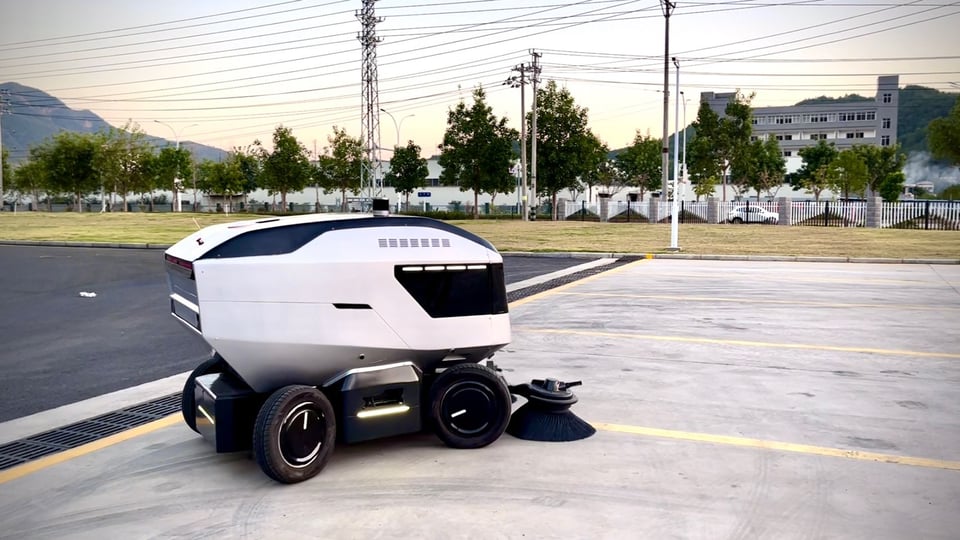
What is the difference between an IMU and an Attitude and Heading Reference System (AHRS)?
While an IMU gathers and delivers extensive motion data, it does not process, filter, or analyze it. An Attitude and Heading Reference System (AHRS), equipped with an additional on-board processing system, does.
AHRSs compute orientation output using advanced sensor fusion algorithms, as well as providing motion data, roll, pitch, and heading (through magnetic referenced yaw). An AHRS combines the signals from the gyroscope, accelerometer, and magnetometer to accurately determine a 3D orientation without drift. AHRSs are suitable for both static and dynamic situations.
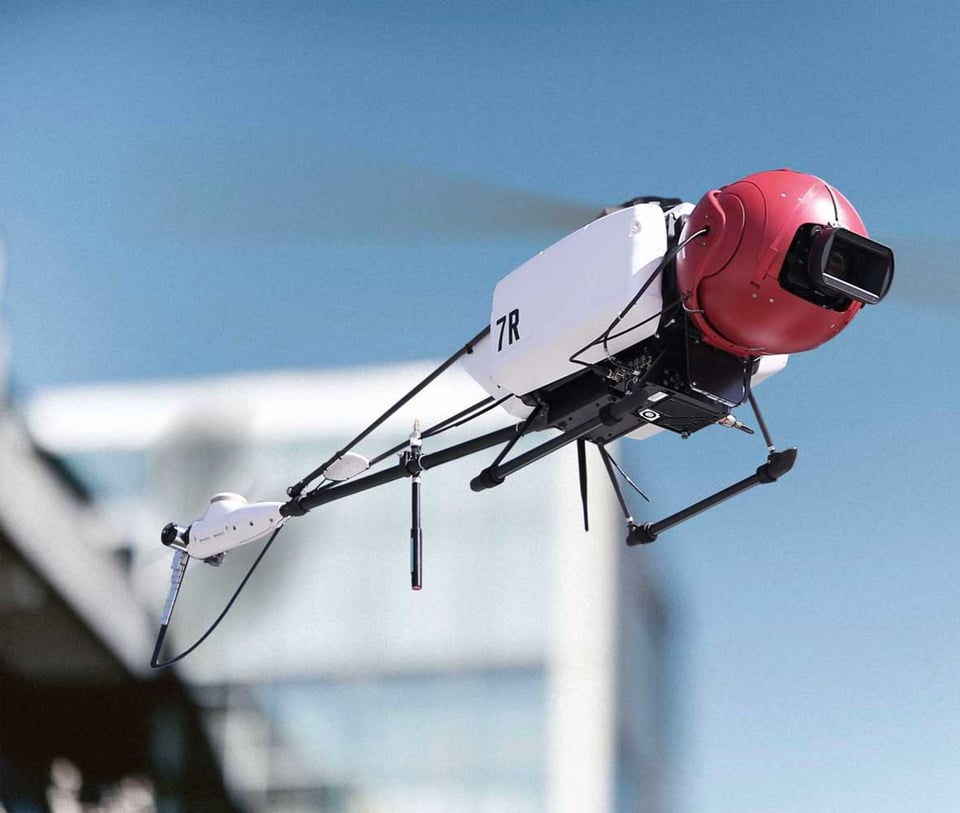
How do 3D gyroscopes work?
Gyroscopes are sensors that measure angular velocity around three axes: roll (X), pitch (Y), and yaw (Z). This capability enables devices to accurately track rotational motion, helping to determine orientation and maintain stability.
Key parameters of gyroscopes
A crucial parameter in any gyroscope is its full range, which dictates the range of motion that can be measured. Below are typical full ranges and their suitable applications:
Typical Full Ranges (deg/s) | Suitable Applications |
450 |
Most industrial applications, including maritime operations, and satellite and camera stabilization |
1000 |
Handheld devices that experience rapid motions |
2500 |
Sports applications, such as analyzing a golf swing which may be performed up to and above 2000 deg/s |
In addition to full range, other important parameters include the gyroscope’s noise level (usually indicated by noise density) and stability over time (indicated by in-run bias stability). Understanding these parameters is important to determine how errors accumulate over time, a phenomenon known as "“drift,"” especially when integrating gyroscope data to calculate orientation.
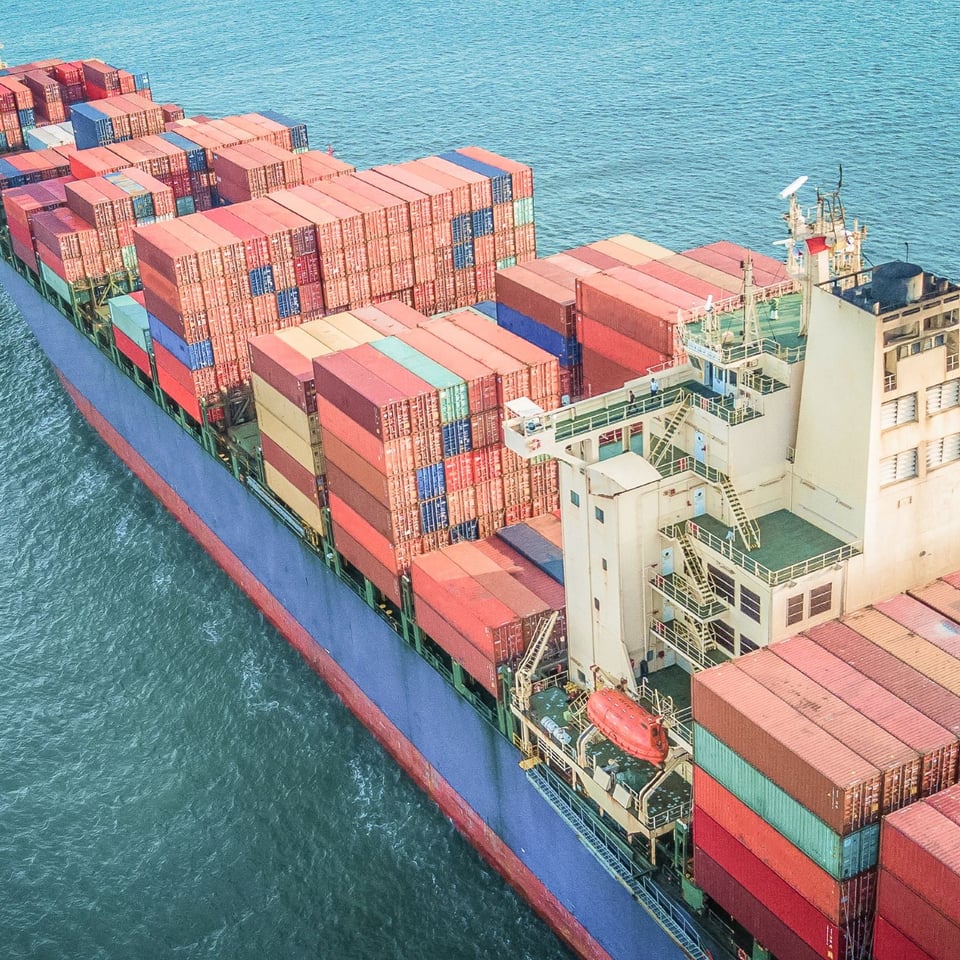
How do 3D accelerometers work ?
Accelerometers are sensors that measure linear acceleration along three axes: X, Y, and Z. Micro-Electromechanical Systems (MEMS) accelerometers contain a damped mass system on a spring, etched in silicon. When the device accelerates, this mass moves, and the movement is measured and converted into acceleration data (in units of g or m/s2).
For short periods, acceleration data can be integrated to estimate both velocity and displacement. Additionally, accelerometers can provide valuable information on the absolute inclination (roll/pitch) of an object by measuring the direction of gravity with respect to the object.
Key parameters of accelerometers
One of the key parameters of any accelerometer is its full range, which determines which motion can be measured. Typical full ranges and suitable applications are listed below:
Full Range (g) |
Suitable applications |
5 |
Applications with lower acceleration requirements |
10 |
Most industrial applications |
20 |
Aerospace and other high-acceleration environments, where extreme movements are frequent |
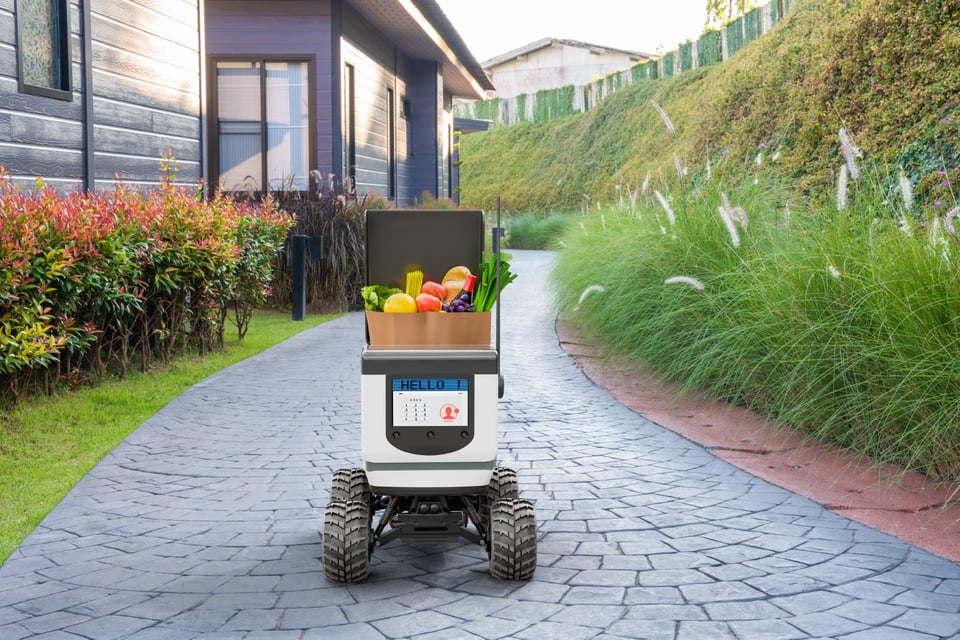
How do 3D magnetometers work ?
Magnetometers are instruments that measure the strength of a magnetic field along three axes: X, Y, and Z. In industrial applications, an IMU’s magnetometers are often used to track the Earth'’s magnetic field. These data are then to estimate an object’s absolute yaw (or ‘heading’) relative to magnetic North. This technology ensures that a wide range of applications, from autonomous vehicles to industrial equipment, can maintain precise directional orientation.
Essential features of a well-designed IMU
your IMU should have a robust signal processing pipeline capable of sampling data from the internal sensors at a high rate, up to several kHz;
the data from your IMU should be synchronizable across a wide variety of calibration parameters such as bias, temperature, sensor alignment, and more;
your IMU should be configurable and easy to integrate, in terms of both hardware and software.
Why use an IMU?
Think of an IMU tracker as the digital equivalent of a human'’s vestibular system. It can offer real-time data on an object'’s movement, orientation, and heading. This data is essential for many industrial tasks, such as stabilizing gimbals, aiming antennas, guiding autonomous vehicles or robots, and more. Additionally, IMUs are a vital component in systems that rely on multiple sensors, such as camera-based tracking for motion capture, lidar-based mapping systems, and GNSS-based localization for accurate positioning. Hear more about IMUs' added value from Meindert Zeeuw.
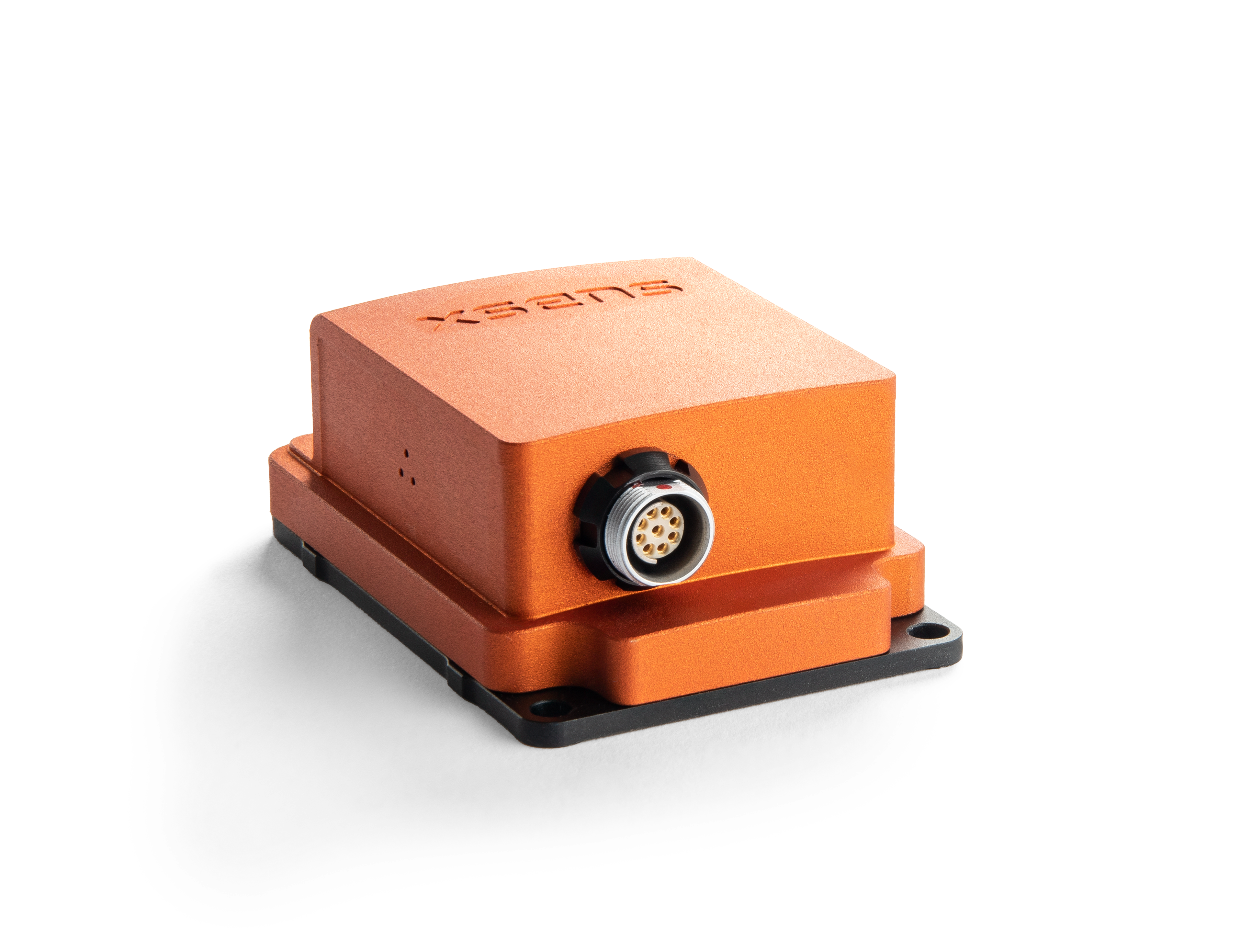
Our IMU solutions
Choosing the right sensing elements will help you to select the right IMU quality for your application. In a market in which sensor prices range from 1 to 1,000 USD, it can be tempting to opt for cheap, low-end solutions. However, to develop industrial-grade systems, the effort and cost of conditioning and processing can be overwhelming. That’s where industrial-grade modules come in: they are not only more cost-effective, but also save time and reduce complexity.
We strike the balance between price and performance, combining premium quality with robust industrial strength. Xsens IMUs often serve as foundational elements for many of our customers, acting as building blocks to allow them to create complex systems tailored to their specific needs.
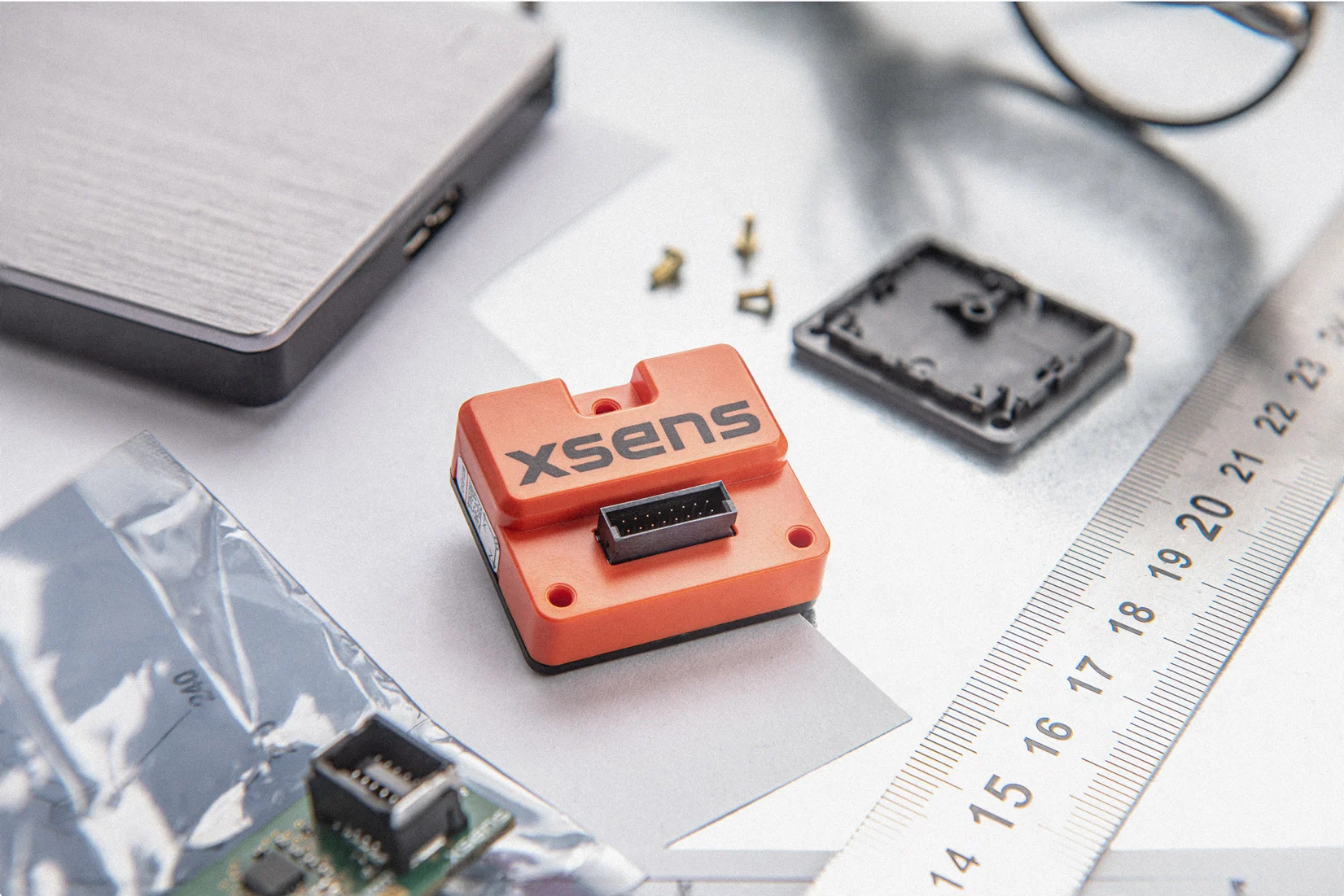
Why choose an Xsens IMU?
When it comes to IMUs, Xsens, a Movella brand, has numerous application and installation advantages:
-
High-quality strapdown integration model, including coning/sculling compensation, antialiasing, and proper filtering
-
Easy configurability of outputs, output rates, output format, and sensor alignment
-
Synchronization options
-
Component end-of-life (EOL) management
-
Fully tested and calibrated
-
Plug-and-play
Sensor modules
Our customers
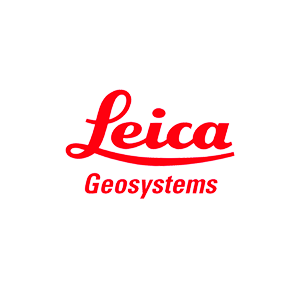
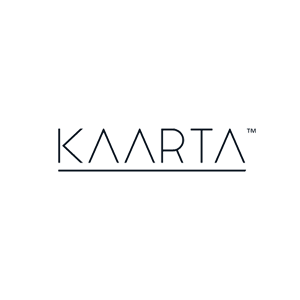
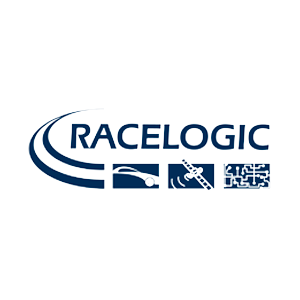
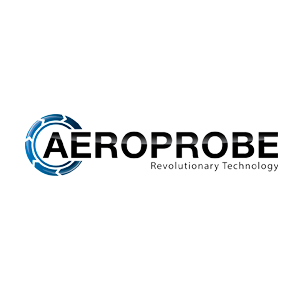
Applications
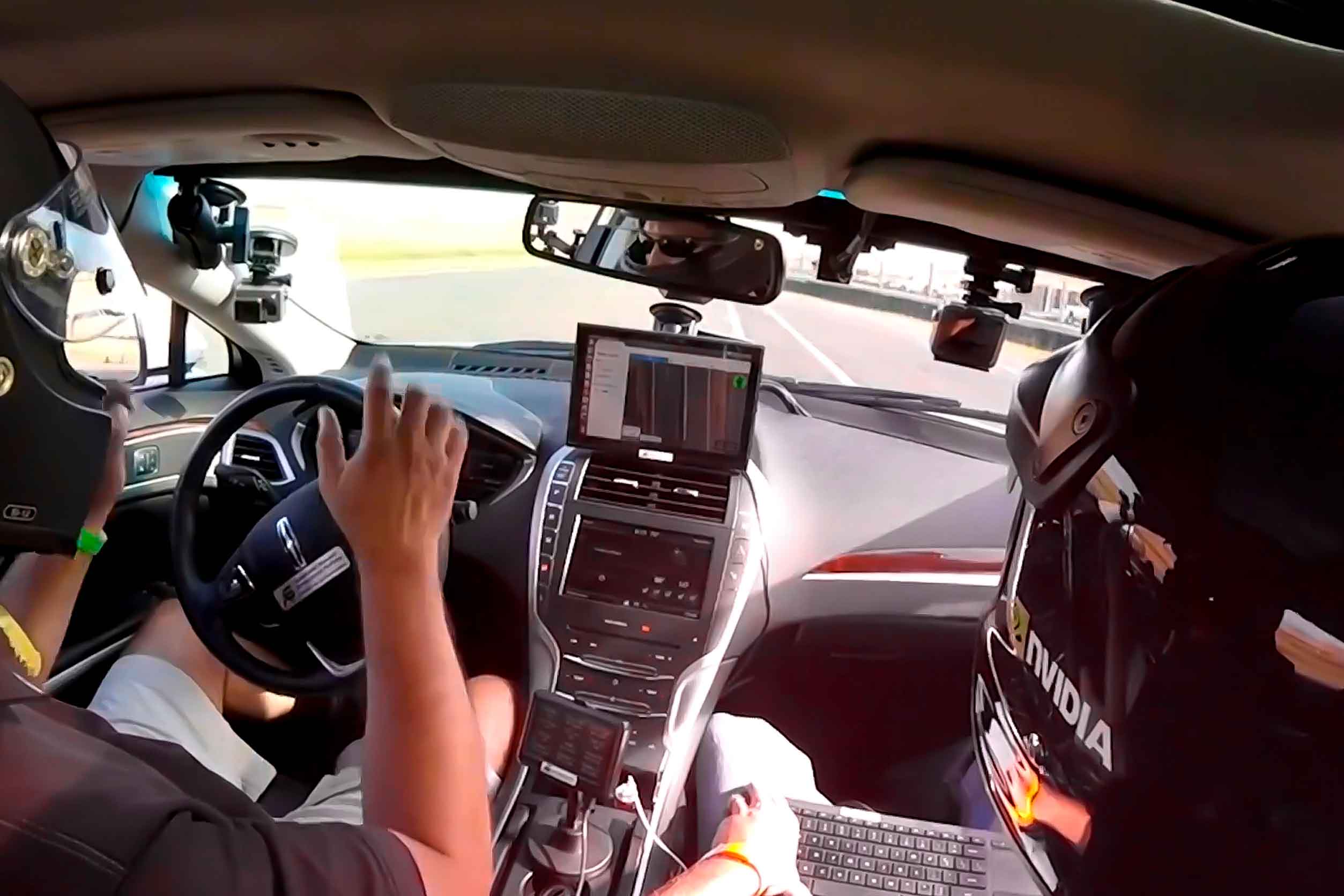

Reliability and precision are of the utmost importance in this field. The robust hardware and software, along with the anti-magnetic distortion filters of the MTi series, make them a highly suitable, stable platform for motion technology applications at sea and in seaports.

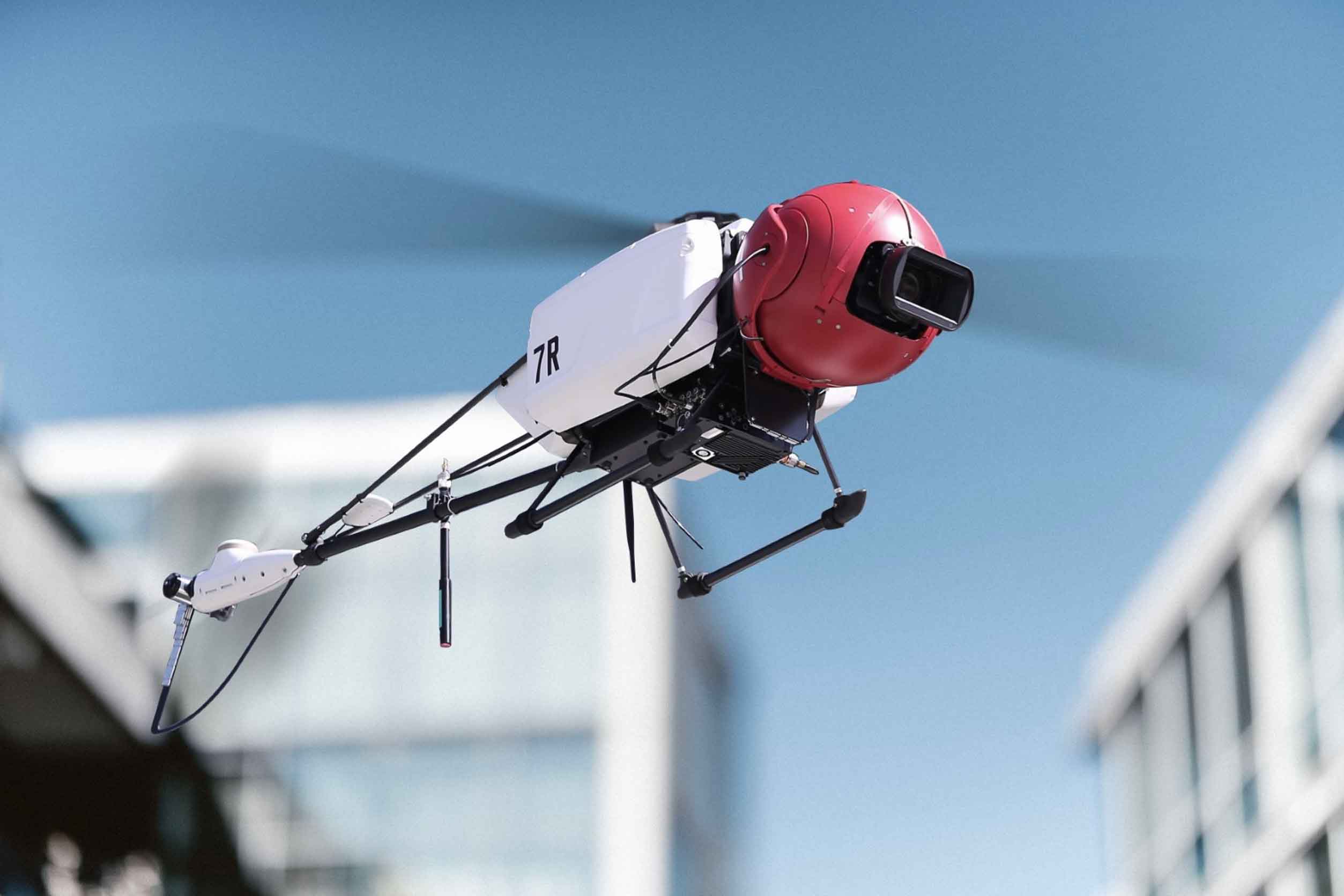
Resources
Newsletter
Sign up here for the Movella newsletter and stay up to date about everything Movella has to offer.
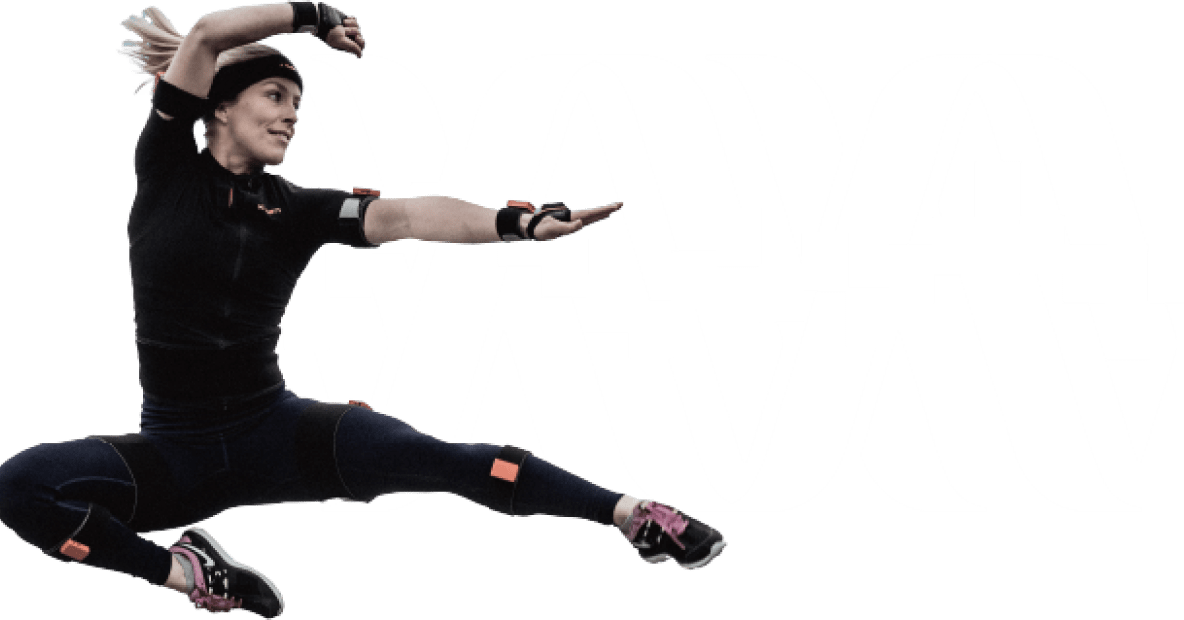